From drawing
to production
Evans Prototype Engineering (EPE), established in 2022, is dedicated to delivering precision-engineered solutions tailored to a wide range of customer requirements. Our expertise spans everything from creating unique, one-off components from sample parts or preliminary sketches to managing full-scale production runs to support your business’s operational needs.
At EPE, we manage the entire engineering process in-house, ensuring every component receives meticulous attention to detail. We build strong, collaborative relationships with our clients, allowing us to deliver precisely what you need—on time and to specification. By drawing on our extensive industry experience, we work closely with you to optimize every project aspect, offering insights that add value to each phase of development.
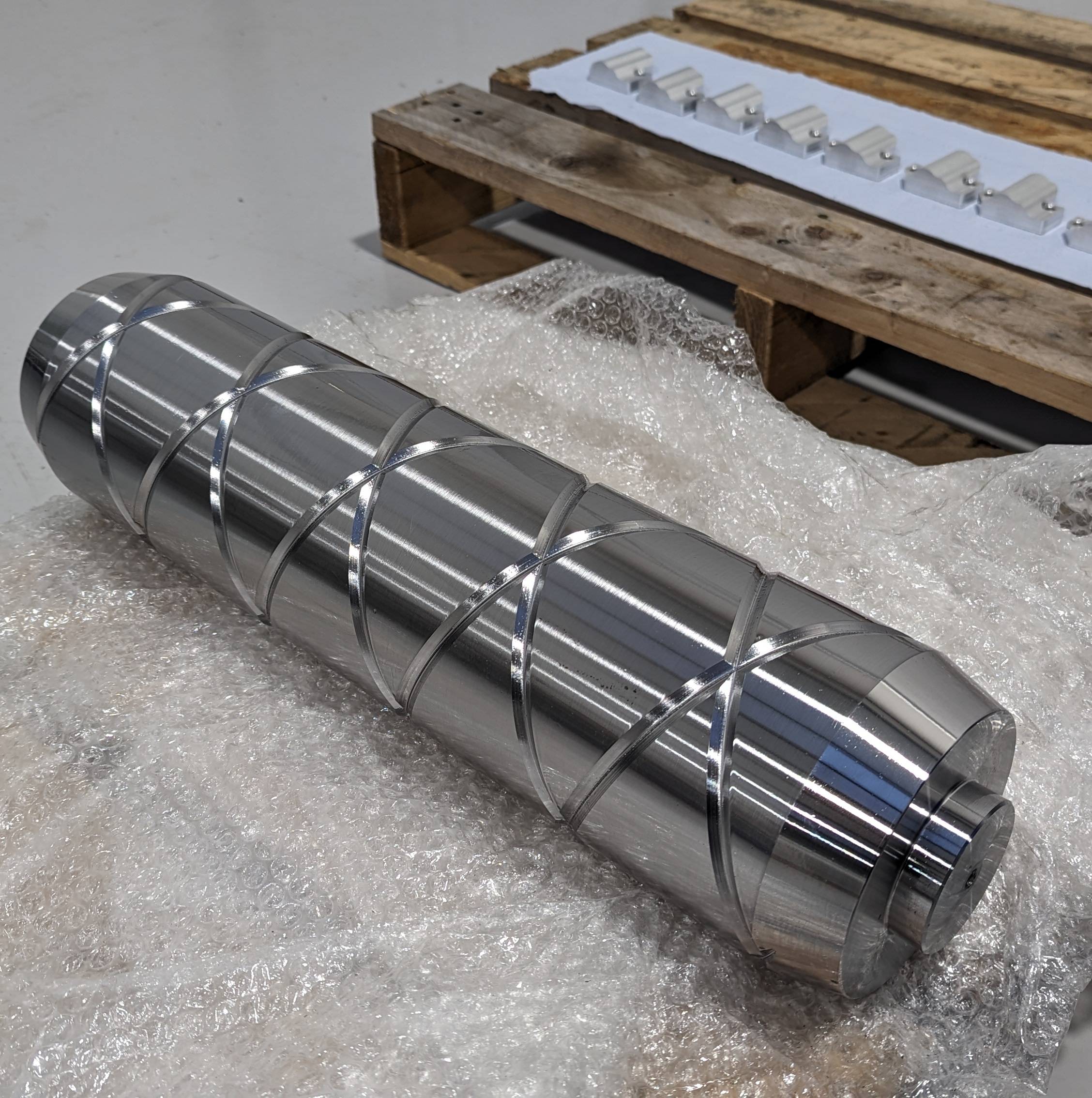
Our commitment to quality and service is demonstrated through the loyalty of our repeat customers, who trust EPE to consistently provide high-quality parts and reliable support.
We support a wide range of sectors throughout the UK
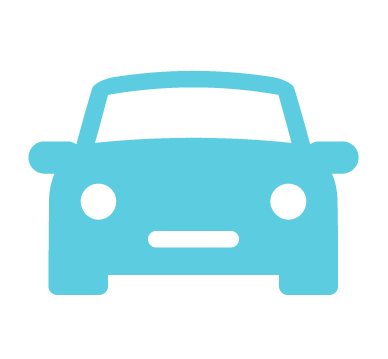
Automotive
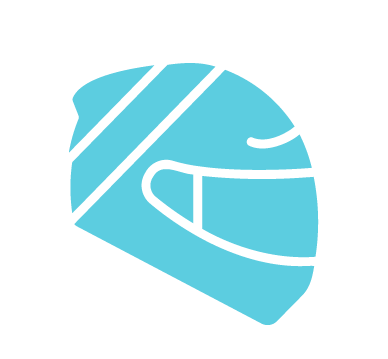
Motorsport
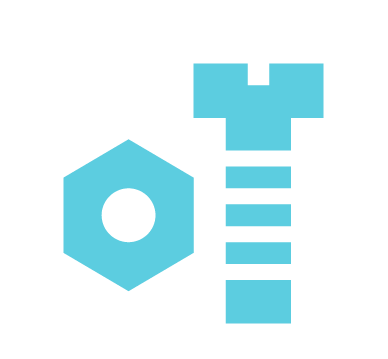
Industrial
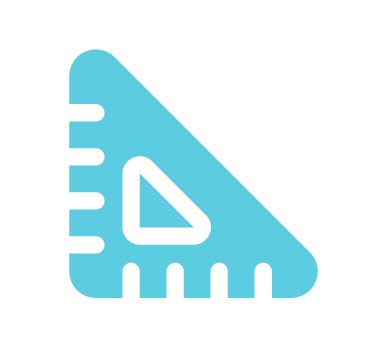
Scientific
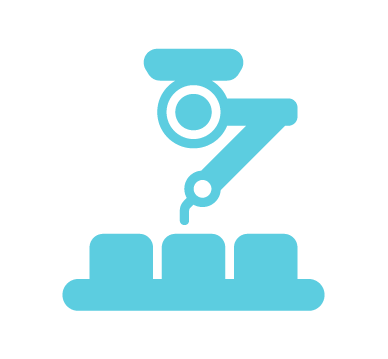
Fabrication
Reverse
engineering
3D scanning is used in house at EPE to provide a basis to generate accurately modelled forms that conventional measurement techniques cannot be used for.
FDM 3D printing: Our Prusa 3D printer has become an essential tool to quickly print prototype parts for the customer to physically fit onto or into assemblies, allowing real world test fitting before we cut any metal. This drastically speeds up the development process and minimises the risk of any errors when the final manufactured product is finished.
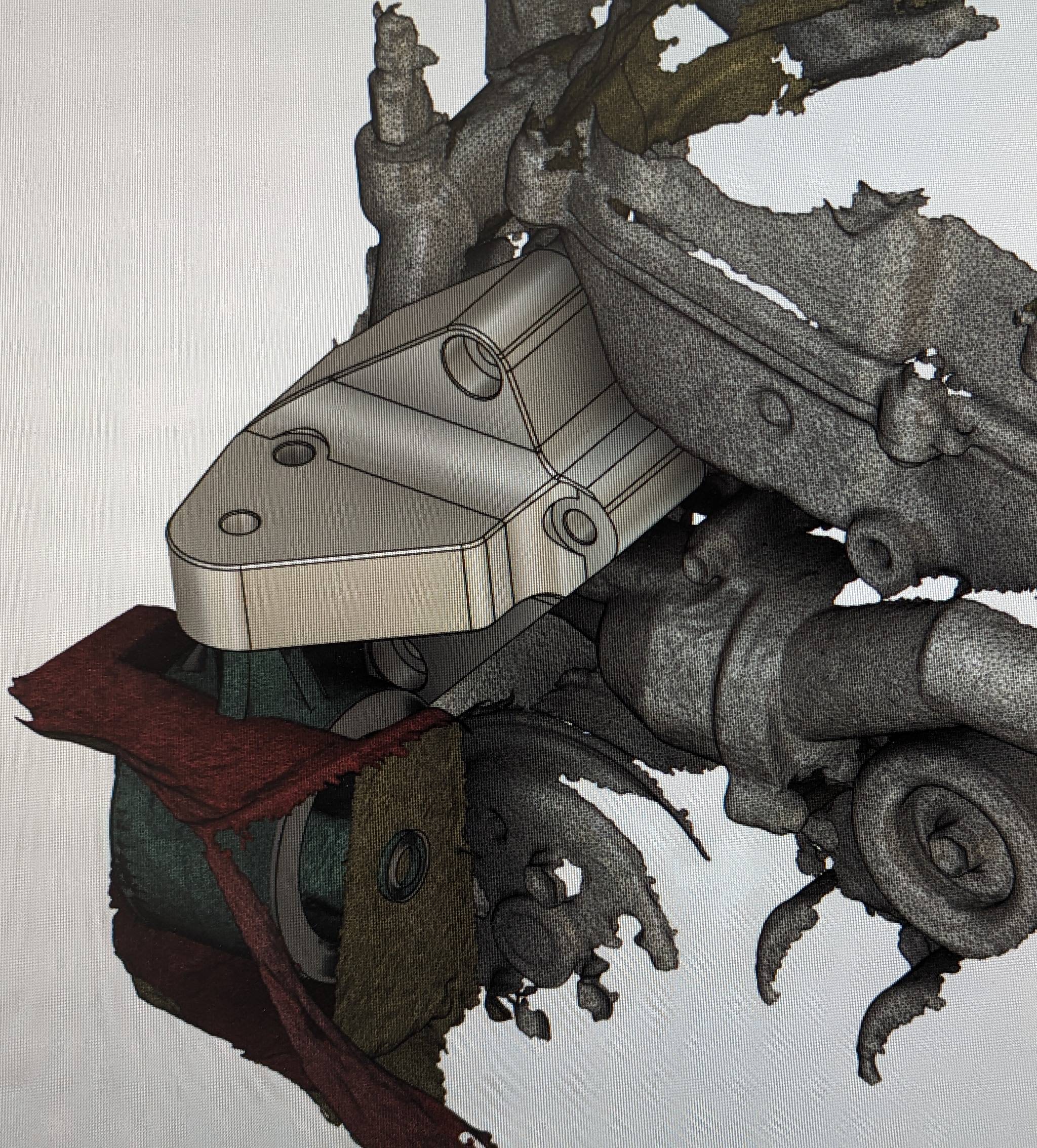
CAD/CAM
Here at EPE we use Autodesk Fusion 360 for all CAD and CAM operations. With this powerful tool we can control all manufacturing activities for our machinery and equipment.
Quality
We use a wide range of digital and analogue measurement tools to ensure exact drawing specs are met on all parts.
Assembly
Many projects designed and manufactured at EPE are not only made in house, but fully assembled and tested before reaching the customer to guarantee perfect fitment and performance in service.
A wide array of
supportive processes
- AC/DC tig welding
- Manual turning
- Bespoke sealing gaskets tooled and cast on-site
- For the specialised services we can’t process in house, we have a network of trusted suppliers to rely on. This means you still have only 1 point of contact to control your project all the way through to delivery.
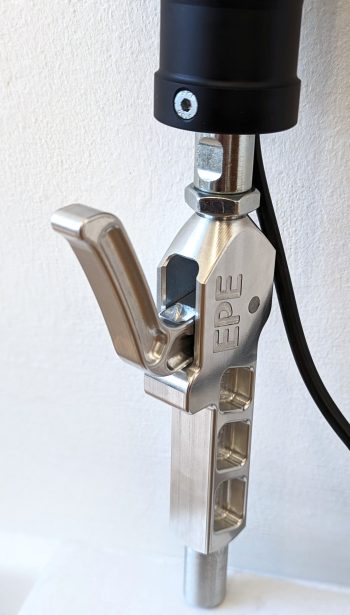